Die Produktion großer Industriebranchen in Deutschland hat sich unter dem Eindruck von Corona-Pandemie und Energiepreisschock in den letzten Jahren sehr unterschiedlich entwickelt. So stieg die Fertigung in der Elektrotechnik gegenüber Anfang 2015 um 18%. In der Chemieindustrie ist im gleichen Zeitraum ein Rückgang um 20% zu verzeichnen. Die Unterscheide sind nicht nur konjunkturell, sondern auch strukturell bedingt. Es wird künftig wichtiger, zwischen dem Industriestandort Deutschland und der deutschen Industrie zu unterscheiden.
Wir schätzen die mittelfristigen Perspektiven der Elektrotechnik am Standort Deutschland recht günstig ein, weil die Branche von einigen Megatrends profitieren wird, die zum Teil staatlich gefördert werden. Dazu zählen die Dekarbonisierung bzw. Elektrifizierung (Klimaschutz/Energiewende) sowie die Digitalisierung, die für zusätzliche Aufträge sorgen.
Neben der Elektrotechnik sind wir auch für den Maschinenbau am Standort grundsätzlich optimistisch. Zwar macht sich seit einigen Monaten bei Aufträgen und Produktion die globale konjunkturelle Abkühlung negativ bemerkbar. Gleichwohl sprechen die Trends in Richtung Robotik und Automatisierung, der globale Ausbau der physischen Infrastrukturen, das Streben nach höherer Ressourcen- und Energieeffizienz und die Verknüpfung des klassischen Maschinenbaus mit digitalen Technologien (Künstliche Intelligenz, Industrie 4.0 usw.) für eine Mehrnachfrage nach modernen Maschinen.
Seit der Corona-Pandemie ist die Volatilität in der Automobilindustrie mit Abstand am stärksten ausgeprägt. Neben den Sondereffekten dürfte die Transformation in der Branche in Richtung Elektromobilität netto zu Wertschöpfungsverlusten am Standort Deutschland führen. Gleichwohl hat die deutsche Autoindustrie gute Chancen beim Kampf um Marktanteile im Bereich E-Mobilität, gerade im Premium-Segment.
Die Chemieindustrie hat den Krieg in der Ukraine mit der anschließenden Energiepreisexplosion sowie dem Stopp direkter russischer Lieferungen von Pipelinegas nach Deutschland besonders schmerzhaft zu spüren bekommen. Wir erwarten, dass ein Großteil des Produktionsrückgangs struktureller Natur ist.
In der Metallindustrie fielen die Schwankungen bei der inländischen Fertigung seit 2015 vergleichsweise gering aus. Innerhalb der Metallindustrie sind wir für die Herstellung von Metallerzeugnissen optimistischer als für die Metallerzeugung. Letztere gerät strukturell durch die hohen Energiepreise unter Druck.
Ein aus wettbewerblichen Gründen ohnehin fragwürdiger vergünstigter Industriestrompreis für energieintensive Branchen dürfte den Verlust an Wertschöpfung am Standort zwar verlangsamen, aber nicht gänzlich aufhalten.
Unterschiedlicher Produktionsverlauf
Der Produktionsverlauf der großen Industriebranchen in Deutschland verlief von 2015 bis zum Beginn der Corona-Pandemie recht gleichförmig. Seither haben die Corona-Krise, der Energiepreisschock sowie strukturelle sektorale Trends zu deutlichen Verwerfungen geführt. Im Vergleich zu Anfang 2015 stieg die Fertigung im dynamischsten Sektor (Elektrotechnik) um real 18%. In der Chemieindustrie ist im gleichen Zeitraum ein Rückgang um 20% zu verzeichnen.
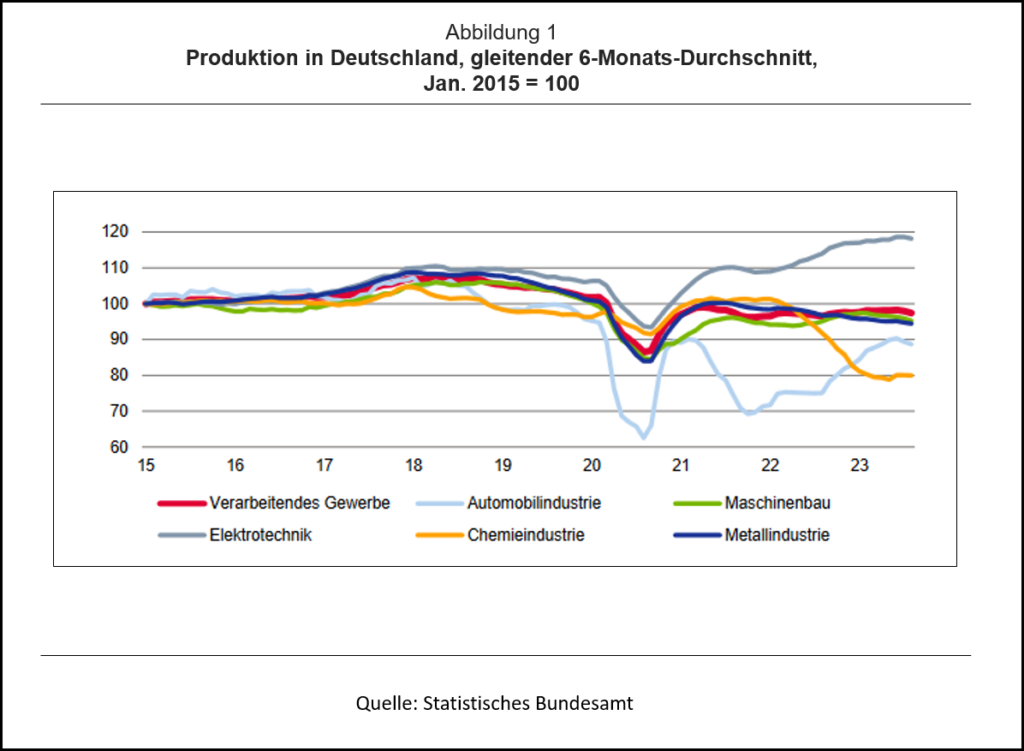
Die Grafik deutet auf einige strukturelle Verschiebungen in der deutschen Industrielandschaft hin:
- Unter den betrachteten Industriebranchen ist es lediglich der Elektrotechnik gelungen, ihre Produktion gegenüber dem Vor-Corona-Niveau zu steigern. In allen anderen Sektoren liegt die Fertigung aktuell (deutlich) unter den historischen Höchstständen, die 2017/18 erreicht wurden. Wir schätzen auch die mittelfristigen Perspektiven der Elektrotechnik am Standort Deutschland recht günstig ein, weil die Branche von einigen Megatrends profitieren wird, die zum Teil staatlich forciert werden. Dazu zählen die Dekarbonisierung bzw. Elektrifizierung (Klimaschutz/Energiewende) sowie die Digitalisierung, die für zusätzliche Aufträge sorgen. Zudem ist die Branche weniger stark von den hohen Energiepreisen in Deutschland betroffen, weil sie nicht energieintensiv produziert.
- Neben der Elektrotechnik sind wir auch für den Maschinenbau am Standort grundsätzlich optimistisch. Zwar macht sich seit einigen Monaten bei Aufträgen und Produktion die globale konjunkturelle Abkühlung negativ bemerkbar. Gleichwohl sprechen die Trends in Richtung Robotik und Automatisierung, der globale Ausbau der physischen Infrastrukturen, das Streben nach höherer Ressourcen- und Energieeffizienz und die Verknüpfung des klassischen Maschinenbaus mit digitalen Technologien (Künstliche Intelligenz, Industrie 4.0 usw.) für eine Mehrnachfrage nach modernen Maschinen. Wie die Elektrotechnik produziert auch der Maschinenbau nicht energieintensiv. Der Branche ist es ferner in den letzten Jahrzehnen gut gelungen, die eigene Position im internationalen Preiswettbewerb durch eine Fokussierung auf hochwertige Spezialmaschinen zu festigen. Auch die Abwertungen von Währungen aus Konkurrenzstaaten gegenüber der D-Mark und dem Euro konnte der deutsche Maschinenbau historisch gesehen zumeist gut abfedern. Nicht zuletzt spricht die mittelständische Struktur des Sektors für eine größere Verbundenheit mit dem Standort Deutschland. Die größte Herausforderung dürfte darin liegen, auch mittelfristig genügend Fachkräfte am Standort Deutschland zu sichern, um in den einzelnen Sparten des Maschinenbaus auch künftig zur Weltspitze zu zählen.
- Seit der Corona-Pandemie ist die Volatilität in der Automobilindustrie mit Abstand am stärksten ausgeprägt. Zu Beginn der Corona-Krise fuhr die Branche die Produktion wegen pandemiebedingten Einschränkungen und in Erwartung einer sinkenden Nachfrage kurzzeitig viel stärker nach unten als andere Sektoren. Die anschließend einsetzende Erholung wurde und wird durch die mangelnde Verfügbarkeit an Vorprodukten (Halbleiter) und andere Störungen der Lieferketten behindert. Zudem blieb die globale Autonachfrage in der gesamten Zeit verhalten. Im Ergebnis wurden in den Jahren 2020 bis 2022 in Deutschland kumuliert gut 5,3 Mio. weniger Pkw produziert als von 2017 bis 2019 (-34,6%). Neben den Sondereffekten dürfte die Transformation in der Branche in Richtung Elektromobilität netto zu Wertschöpfungsverlusten am Standort Deutschland führen. Gerade bei Zulieferern, die Teile und Komponenten für Autos mit Verbrennungsmotor herstellen, dürften Produktionskürzungen nicht zu vermeiden sein. Gleichwohl hat die deutsche Autoindustrie gute Chancen beim Kampf um Marktanteile im Bereich E-Mobilität, gerade im Premium-Segment. Eine aktuelle ifo-Untersuchung zeigt, dass deutsche Unternehmen in Sachen Innovationsfähigkeit und Qualifikationsniveau der Beschäftigten sehr gut positioniert sind.[1] Unabhängig vom Trend in Richtung E-Mobilität dürfte es aus Kostengründen künftig schwerer fallen, Autos im Volumensegment in Deutschland zu bauen. Insofern halten wir eine Rückkehr des Produktionsniveaus zu früheren Höchstständen für unwahrscheinlich.
- Die Chemieindustrie hat den Krieg in der Ukraine mit der anschließenden Energiepreisexplosion sowie dem Stopp direkter russischer Lieferungen von Pipelinegas nach Deutschland besonders schmerzhaft zu spüren bekommen. Am aktuellen Rand liegt die Produktion in der Branche um 23,6% unter dem Höchstwert von Ende 2017. Wir erwarten, dass ein Großteil dieses Rückgangs struktureller Natur ist. Auch andere energieintensive Branchen wie die Baustoff- und die Papierindustrie (nicht in der Grafik abgebildet) haben in den letzten Quartalen deutliche Fertigungsrückgänge hinnehmen müssen, die im Falle der Baustoffindustrie aber auch mit der schwachen Baukonjunktur zu erklären sind. Ein aus wettbewerblichen Gründen ohnehin fragwürdiger vergünstigter Industriestrompreis für energieintensive Branchen dürfte den Verlust an Wertschöpfung am Standort zwar verlangsamen, aber nicht gänzlich aufhalten. Dafür dürften die energie- und klimapolitischen Perspektiven zu ungewiss sein und die erwartete Differenz bei den Energiepreisen im Vergleich zu anderen Ländern (inklusive USA und China) zu groß bleiben.
- In der Metallindustrie fielen die Schwankungen bei der inländischen Fertigung seit 2015 vergleichsweise gering aus. Die schwächere Konjunktur und höheren Energiepreise spiegeln sich aber seit Anfang 2021 in einer tendenziell sinkenden Produktion wider. Innerhalb der Metallindustrie sind wir für die Herstellung von Metallerzeugnissen optimistischer als für die eigentliche Metallerzeugung. Letztere gerät strukturell durch die hohen Energiepreise unter Druck. Wir halten es für wenig wahrscheinlich, dass bei der angestrebten grünen Transformation der Metallerzeugung alle Kapazitäten am Standort erhalten werden können. Dies gilt z.B. für die geplante Umstellung der Stahlproduktion auf grünen Wasserstoff. Wegen globaler Überkapazitäten in der Branche, der hohen Energiepreise in Deutschland sowie wegen der Ungewissheit bezüglich der physischen Versorgung mit grünem Wasserstoff dürfte die mengenmäßige Stahlproduktion in den kommenden Jahren tendenziell sinken. Auch staatliche Subventionen für die Transformation dürften diese nicht gänzlich verhindern, zumal die finanzielle Leistungsfähigkeit des Staates begrenzt ist. Zwar wird auch künftig in Deutschland noch Stahl produziert. Es zeichnet sich aber ein niedrigeres und ggf. sinkendes Niveau ab. 2022 lag die mengenmäßige Stahlerzeugung in Deutschland um 15% unter dem Wert von 2017.
Strukturwandel auch durch Regulierung ausgelöst
In der deutschen Industrie ist ein Strukturwandel im Gange, der sich in den kommenden Jahren weiter beschleunigen könnte. Es wird (relative) Gewinner und Verlierer geben. Grundsätzlich ist industrieller Strukturwandel nichts Neues – und auch nichts Negatives. So spielte die Textil- und Bekleidungsindustrie in früheren Jahrzehenten eine deutlich größere Rolle am Standort Deutschland als heute. Aufgrund von Lohnkostenunterschieden verlagerte aber z.B. die Bekleidungsindustrie schon früh ihre Produktion an Standorte mit niedrigeren Löhnen.
In der Folge kamen Konsumenten in Deutschland in den Genuss niedrigerer Preise für Bekleidung. In diesem Strukturwandel hat sich die Textilindustrie im Laufe der Jahrzehnte stärker auf sogenannte technische Textilien konzentriert, bei denen Innovationskraft gefragt ist. Hier sind deutsche Unternehmen gut positioniert, und eine Fertigung in Deutschland lohnt sich nach wie vor. Ein weiteres Beispiel für einen langfristigen Strukturwandel ist die Konsumelektronik. Hier wird der Großteil der in Deutschland abgesetzten Produkte nicht vor Ort, sondern im Ausland (Asien) produziert, wo die Produktionsbedingungen günstiger sind.
Solche strukturellen Verschiebungen waren in der Vergangenheit häufig ein Marktergebnis (z.B. Lohnkostenunterschiede). Der künftige Strukturwandel dürfte aber in Teilen auch durch unterschiedliche regulatorische Rahmenbedingungen ausgelöst werden. Dazu zählen nicht zuletzt die Energie- und Klimapolitik, einerseits mit ihrem Einfluss auf die Energiepreise und die Versorgungssicherheit und andererseits mit klimapolitisch motivierten Subventionen, die eine Fertigung in Deutschland fördern sollen.
Wir rechnen damit, dass der Anteil des Verarbeitenden Gewerbes an der gesamten Bruttowertschöpfung in den kommenden Jahren weiter sinken wird. 2016 lag er bei 22,9%. Im letzten Jahr waren es 20,4%. Es wird künftig wichtiger, zwischen dem Industriestandort Deutschland und der deutschen Industrie zu unterscheiden. Deutschlands Position im internationalen Wettbewerb hat sich bei klassischen Standortfaktoren wie der Steuerbelastung von Kapitalgesellschaften, Lohnhöhe, Energiekosten, digitale Infrastruktur oder der Flexibilität bei Arbeitszeiten eher verschlechtert. Zwar ist Deutschland noch immer eine hohe Innovationskraft zu bescheinigen.[2] Ungünstige wirtschaftliche Rahmenbedingungen sind jedoch eine Bürde für die nähere Zukunft. Dagegen können gerade große Industrieunternehmen im Laufe der Zeit ihre Produktionsstandorte nach ihren individuellen Kosten- und Kundenstrukturen gestalten.
[1] Vgl. CESifo (2023). Green Skills in German Manufacturing. EconPol Policy Brief 55/2023
[2] Vgl. Möbert, Jochen und Julius Schumann (2023). Germany’s competitiveness between pioneer and laggard